- Thermocouples
- Screw-in thermocouple
- Plug-in thermocouple
- Dipstick-Thermocouples
- Wire thermocouple
- Sheathing-tube thermocouples
- Sheathed thermocouple
- Surface thermocouple
- Screw-in resistance thermometer
- Plug-in resistance thermometer
- Wire resistance thermometer
- Sheating tube resistance thermometer
- Sheathing resistance thermometer
- Accessories Thermocouples
- Surface resistance thermometer
- Sheathed thermocouple with terminal head
- Thermo connectors
- More products
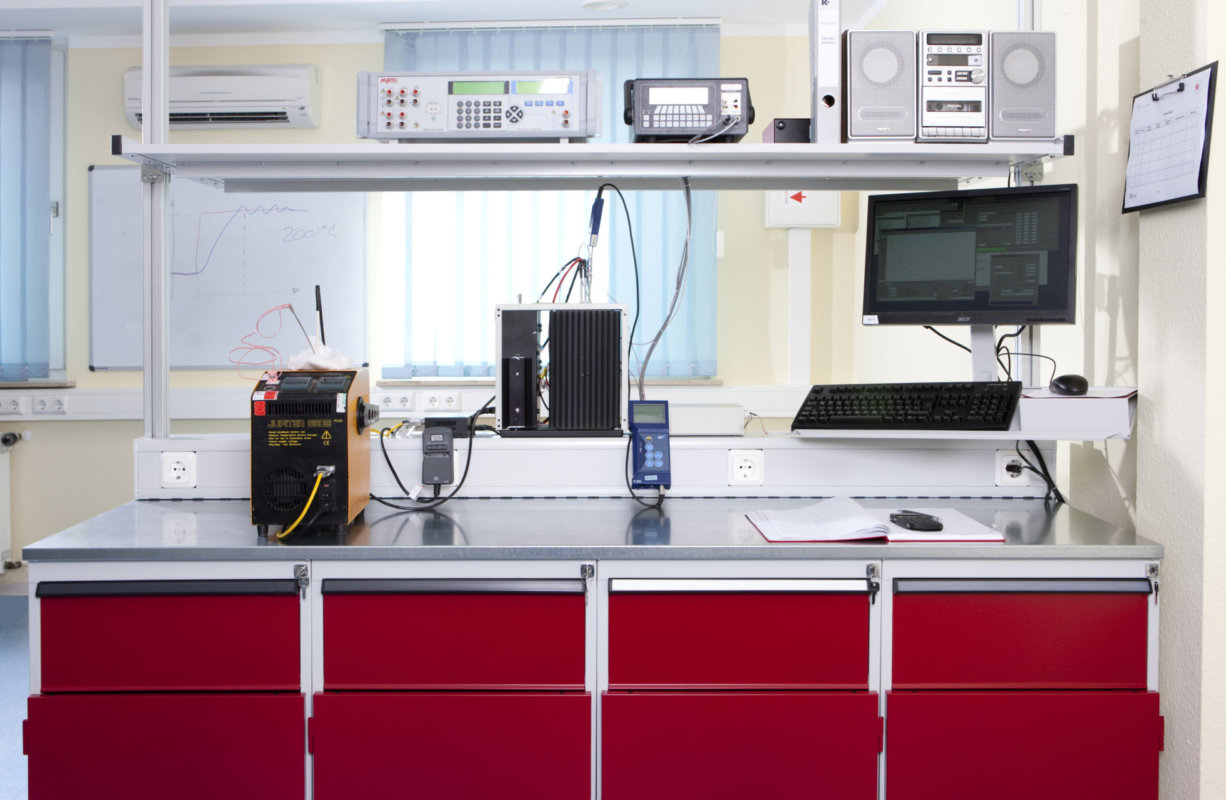
Thermocouple calibration
Calibrate thermocouples – Get adviceThermocouples and resistance thermometers are used worldwide when it comes to measuring temperatures. Calibration of thermocouples and resistance thermometers determines the measurement deviation of the test item from the true value of the measurand. Calibration uses two methods: Fixed point calibration and comparison calibration. Calibration of a thermocouple involves measuring the thermoelectric voltage relative to a reference junction temperature of 0 °C. To calibrate resistance thermometers, the resistance is measured at the calibration temperature. All process critical measurements must be checked for accuracy. Calibration checks instruments whether they are within the allowed tolerance.
A regular calibration of thermocouples and resistance thermometers is recommended because the accuracy could change because of thermal stress and mechanical stress. Corrosion and damage can also cause deviations. The standard calibration method for industrial thermocouples and resistance thermometers is the comparison calibration, where the temperature points can be chosen for the specific application.
The calibration at fixed temperature points is the more precise calibration. The temperature probe will be compared with natural temperature fix points, as an example the water triple point. The ITS-90 temperature scale is defined by natural fixed temperature points, to make temperatures international more comparable. More fixed temperature points are gallium melting point (29,7646°C), silver solidification point (961,78 °C).
Calibration according to DakkSGermany’s national accreditation body is an authority of the Federal Republic of Germany and responsible for the accreditation of the test laboratories. The current valid norm for testing and calibrating is DIN EN ISO/IEC 17025:2018. A calibration according to DakkS stands for a calibration by an accredited laboratory with traceability to national and international standards. The results of the calibration are documented in a certificate containing information on the measurement uncertainty and traceability chains.
DAkkS calibration is an important quality assurance tool that helps to ensure the accuracy of measurements. We are certified according to the quality management system ISO 9001:2015 certified, ensuring the quality of the elements.
We offer:
- Calibration according to DAkkS
- Resistance thermometers from -196°C to +960°C
- Thermocouples from -196°C to +1200°C
- Precious metal thermocouples from -196°C to +1200°C
- Fixed point calibration
ISO 9001:2015
Certified development, production and distribution of temperature sensors and their accessories

Calibrate thermocouples
With precision for best resultsThese thermometers have different designs, each optimized for different measurement conditions. A distinction is made between connection types, sensor types and metal or semiconductor resistors. The purpose of metal resistors is to have the highest possible temperature coefficient. This means that a change in temperature causes the greatest change in electrical resistance. Platinum has very good properties to achieve this effect. Nickel allows more accurate measurements, but has a lower temperature range. The lowest possible measuring current is introduced via connecting leads made of copper or nickel. The voltage drop is then measured and the resistance determined according to Ohm’s law.
Thermocouples are normally used at high temperatures, so the temperature resistance should be checked before use. To transmit the signal to the measuring instrument, you have to use a thermo- or compensating wire, produced from the same material like the thermocouple conductor. With thermocables, thermoelectric voltages only occur when they are connected to the device.
Factory calibration
Our in-house calibration briefly explained
We offer you the option of creating a factory calibration of your configured temperature sensor. We offer this cost-effective, fast and efficient form of calibration in the range from -35°C to +660°C. The calibration is carried out using a comparison method in a metal block calibrator. The test points must always be within the measuring range. The minimum immersion depth of the sensors is 150 mm. You are also welcome to send your temperature sensors to us for regular inspection.
Take a look at our sample calibration certificate here.
The measurement uncertainty to be achieved for thermocouples of type K, J, N, T depends on the temperature range and the test object.
- From -35°C to +35°C: ±1,5 K
- From +35°C to +400°C: ±1,6 K
- From +400°C to +660°C: ±2,0 K
If you need a calibration in a different measuring range or with a DAkkS certification, please contact us.
We would be happy to advise you on which calibration is best for your application.
Thermocouple calibration
Handemade in Germany
In our factory in Lindlar, Germany, we manufacture high-quality thermocouples in all thermocouple types according to DIN EN 60584, resistance thermometers in class AA, A or B according to DIN EN 60751 and NTC or PTC temperature sensors. Thermocouples are used in many different situations and industries. Accordingly, they are widely used in industry and technology. A typical temperature range for the use of thermocouples is -200 to 1200 °C. The strengths of thermocouples are therefore particularly evident where very high temperatures and temperature fluctuations can occur in certain production environments.
Thus, type N thermocouples can be designed for use in harsh environments with high mechanical stress. In such environments, thermocouples can be used to accurately measure temperature and adjust temperature as needed. Because of their versatility, thermocouples come in many different sizes and styles. No patented solution for temperature measurement in industry and industrial production. Requirements vary greatly depending on the production environment.
To ensure optimal temperature measurement, the measurement method should always be adapted to the individual processes in the measurement environment. However, RTDs and thermocouples of various types have become two of the most popular measurement techniques in this field due to their wide range of applications. A key advantage of thermocouples is their robustness to mechanical stress. This is not uncommon in industrial production. Shock, vibration and other disturbance factors that can occur in these environments are well tolerated by the robust design of the elements.
Another advantage is that thermocouples can be constructed with very small measuring points, resulting in a very short response time to temperature. Short-term temperature changes can be detected in the range of a few milliseconds. Thermocouples do not require a power supply, therefore no self-heating of the device.

Calibration temperature measuring instruments
Precise measurement in all areasAll equipment used for process critical measurements should be checked regularly for accuracy. If adjustments are possible, out-of-specification equipment should be brought back into tolerance. If this is not possible, the deviation or measurement uncertainty should be recorded. Then you must decide if the instrument is suitable for its intended purpose. In temperature measurement, the properties of bimetallic and thermocouple wires change over time, especially when used at high temperatures. Other influences such as corrosion and mechanical damage can also age thermocouples and affect measurement accuracy. RTDs and thermistors are sensitive measuring devices and can be easily damaged. Regular testing is therefore essential.
The frequency of gauge calibration is at the discretion of the user in accordance with quality standards. However, during the audit, the auditor will request plausible justification for the chosen audit interval. There are many aspects to consider when deciding how often to calibrate. Appropriate procedures should be defined if the device exceeds acceptable limits as a result of calibration. This also applies to recalls of products manufactured since the last calibration. Such costs should also be taken into account when considering the optimum calibration interval.